Welding Inspection Service: Guaranteeing Compliance and Toughness
Browsing the Globe of Welding Providers: A Comprehensive Overview to Kind and Advantages
In the realm of industrial applications and building and construction jobs, the relevance of welding services can not be overstated. As we begin on this thorough guide to the types and advantages of welding solutions, we will dig right into the intricacies of numerous welding processes, reveal the benefits of MIG and TIG welding, and lost light on the specialized methods that provide to unique tasks.

Various Types of Welding Procedures
Various methods are utilized in welding procedures to sign up with materials together successfully and firmly. One common welding method is Protected Steel Arc Welding (SMAW), additionally referred to as stick welding. This process uses a flux-coated consumable electrode to create the weld. SMAW is flexible and can be utilized in different placements, making it preferred in building and repair.
An additional extensively utilized technique is Gas Steel Arc Welding (GMAW), or MIG welding. In this procedure, a cord electrode is fed through a welding weapon, which likewise releases a securing gas to secure the weld from impurities airborne. GMAW is known for its rate and simplicity of use, making it appropriate for manufacturing and auto markets.
Additionally, Gas Tungsten Arc Welding (GTAW), or TIG welding, is favored for its precision and clean welds. If required, TIG welding makes use of a non-consumable tungsten electrode and a separate filler product. This technique is typically used in aerospace, auto, and creative applications due to its capacity to produce premium welds
Benefits of MIG Welding
MIG welding, likewise called Gas Metal Arc Welding (GMAW), offers unique advantages over various other welding processes, making it a favored selection in production and automotive sectors. One of the main benefits of MIG welding is its convenience. This procedure can be used on a large range of thicknesses and metals, consisting of aluminum, stainless-steel, and moderate steel. In addition, MIG welding is known for its high welding rates, causing enhanced performance. The procedure is fairly very easy to learn and carry out, making it appropriate for both newbies and experienced welders.
Moreover, MIG welding produces tidy welds with marginal spatter, lowering the requirement for substantial post-weld cleaning. Making use of a shielding gas in MIG welding secures the weld pool from impurities in the atmosphere, resulting in premium, solid welds. One more benefit of MIG welding is its capacity to be automated, permitting for consistent and precise welds in mass manufacturing setups. On the whole, the benefits of MIG welding make it a preferred selection for numerous applications where performance, quality, and simplicity of use are vital.
Advantages of TIG Welding
Tungsten Inert Gas (TIG) welding, likewise referred to as Gas Tungsten Arc Welding (GTAW), stands apart in the welding industry for its precise control and high-quality welds. One of the primary advantages of TIG welding is its capability to produce tidy and cosmetically pleasing welds without the demand for filler material. This results in welds that call for very little post-weld cleaning and polishing, making TIG welding perfect for applications where look is important.
Additionally, TIG welding is well-suited for welding slim materials due to its reduced warm input and specific control over the welding arc. This makes it a recommended selection for sectors such as aerospace, vehicle, and electronic devices, where welding slim areas without distortion is necessary.

Exploring Arc Welding Methods
When delving into the world of welding techniques, one comes across a diverse array of arc welding methods that play an important function in different industrial applications. Arc welding is a widely used welding process that includes creating an electrical arc between the base and an electrode material to thaw and join steels. Welding Inspection Service. One of the most common arc welding methods is Secured Metal Arc Welding Visit Your URL (SMAW), additionally called stick welding, which is favored for its flexibility and simpleness. SMAW appropriates for welding thick products and can be used both inside and outdoors, making it a prominent choice in building and pipe welding.
One more widespread arc welding method is Gas Metal Arc Welding (GMAW), commonly referred to as MIG (Metal Inert Gas) welding. GMAW makes use of a palatable wire electrode and a securing gas to protect the weld pool from climatic impurities, causing premium welds with very little spatter. This method is commonly utilized in automobile, manufacturing, and construction sectors for its performance and convenience of use. Generally, arc welding strategies supply a range of options to deal with diverse welding needs across numerous sectors.
Comprehending Specialized Welding Solutions
Specialized welding solutions play an important function in fulfilling the one-of-a-kind needs of complex industrial jobs and precision applications. These services exceed standard welding methods to attend to certain obstacles that typical approaches might not successfully fix. Specialty welding encompasses a large range of sophisticated processes tailored to meet the needs of specialized sectors such as aerospace, vehicle, and manufacturing.
One key aspect of specialized welding services is the ability to deal with unique materials that require customized expertise and devices. This consists of welding processes for products like titanium, magnesium, and different high-strength alloys, which demand a high degree of skill and accuracy to make sure optimal outcomes.
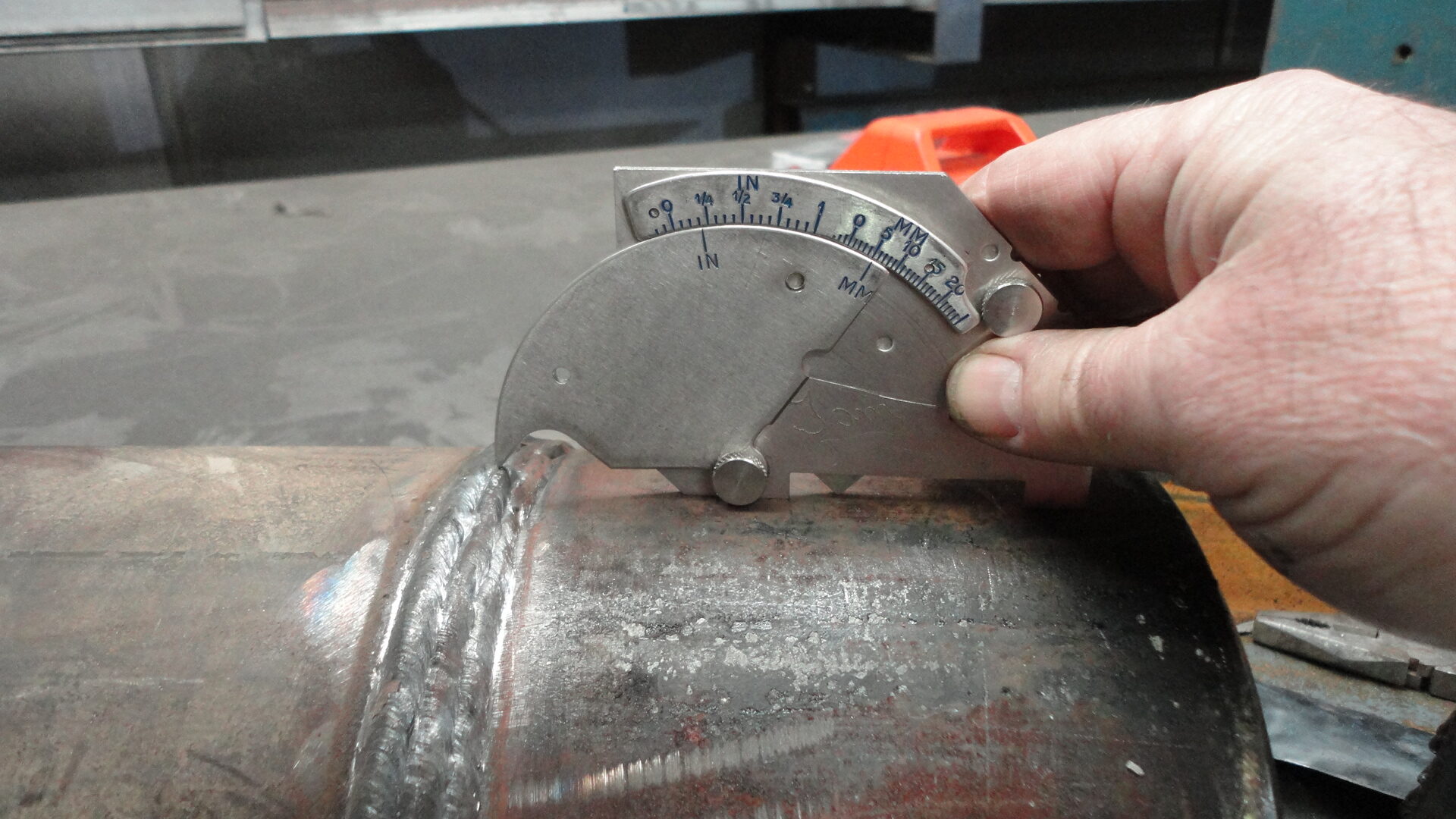
Basically, specialized welding services are important for industries that require the greatest standards of top quality, toughness, and accuracy in their welding tasks. By leveraging specialized strategies and competence, these solutions enable businesses to deal with complex obstacles and accomplish exceptional results in their operations.
Verdict
In verdict, understanding the numerous types of welding procedures and their advantages is crucial for navigating the world of welding solutions. Exploring check arc welding methods and specialized welding services can additionally broaden the alternatives and capabilities available for different welding tasks.
As we embark on this detailed overview to the types and benefits of welding services, we will dig right into the intricacies of various welding processes, discover the benefits of MIG and TIG welding, and lost light on the specialized techniques that cater click here to read to special tasks. One usual welding method is Protected Steel Arc Welding (SMAW), additionally recognized as stick welding.MIG welding, additionally known as Gas Metal Arc Welding (GMAW), provides unique advantages over various other welding processes, making it a preferred option in manufacturing and vehicle sectors.Tungsten Inert Gas (TIG) welding, additionally recognized as Gas Tungsten Arc Welding (GTAW), stands out in the welding industry for its exact control and top quality welds.One more common arc welding technique is Gas Steel Arc Welding (GMAW), commonly referred to as MIG (Metal Inert Gas) welding.